
How AI is impacting smart manufacturing
AI-driven technologies are fueling smart manufacturing and changing the face of the industry as we know it.
From improving production efficiency to enabling predictive maintenance and real-time quality control, AI is helping reduce costs and increase overall productivity.
To this end, it’s worth investigating how manufacturing leaders are leveraging AI and what to expect moving forward.
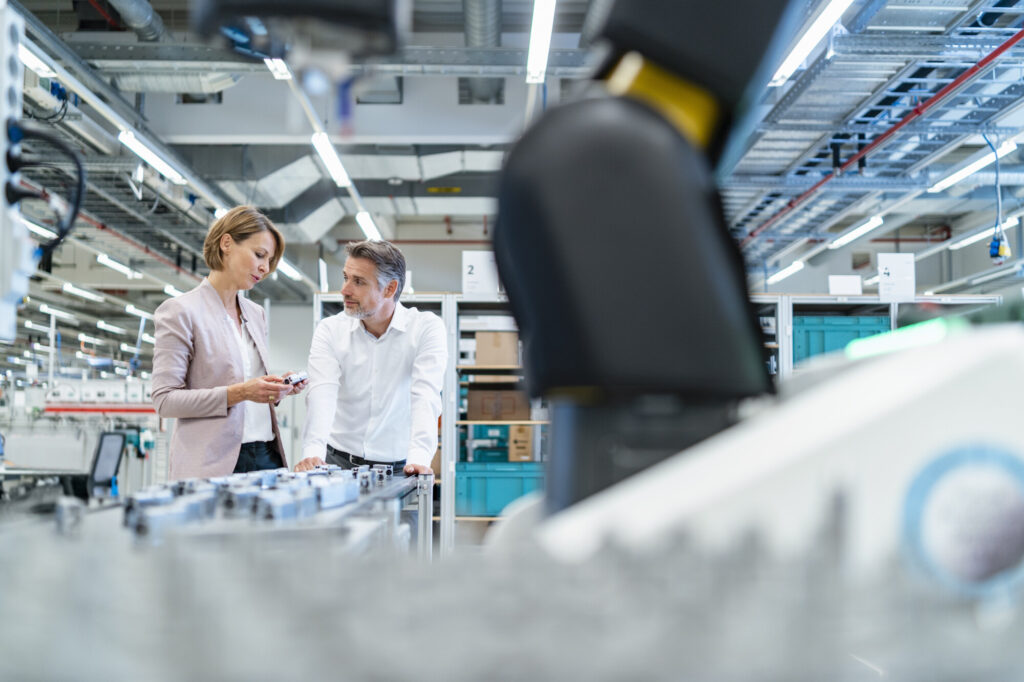
What is a smart factory?
A smart factory is a digitally integrated manufacturing environment powered by AI, automation, and interconnected systems.
In the new manufacturing landscape, adopting smart manufacturing principles is essential for survival, profitability, and growth.
According to McKinsey research, companies transitioning to smart factory systems report significant reductions in operating costs and improvements in product quality and customer satisfaction.
“Implemented successfully, these solutions deliver irresistible returns. Across a wide range of sectors, it is not uncommon to see 30 to 50 percent reductions in machine downtime, 10 to 30 percent increases in throughput, 15 to 30 percent improvements in labor productivity, and 85 percent more accurate forecasting,” the research notes.
Core components of smart manufacturing
Manufacturing leaders need to be practical about how they leverage smart manufacturing, and that means understanding its foundational elements.
AI, for one, enables real-time predictive analytics for equipment monitoring, proactive maintenance, and quality management. Automotive companies such as Toyota and BMW leverage AI-driven predictive maintenance to significantly reduce downtime.
There’s also advanced robotics and automation. Robotics eliminate manual errors and dramatically enhance productivity. These technologies streamline repetitive tasks, while collaborative robots safely complement human operators, improving efficiency in assembly lines.
Benefits of smart manufacturing
Manufacturing leaders considering smart factory integration can expect three primary strategic benefits.
- Increased operational efficiency: Predictive analytics and real-time monitoring reduce downtime, directly enhancing productivity. In a recent discussion with Forbes, an Amazon chief technologist said the company improved storage density by 40% using robotics and automated sorting systems.
- Significant cost savings: Automation significantly lowers labor costs, reduces errors, and optimizes inventory management. Siemens found that companies using predictive maintenance cut maintenance costs by 40%, increased staff productivity by 55%, and decreased the amount of time a machine is unavailable for maintenance by 50%.
- Enhanced product quality and customer satisfaction: Real-time analytics and automated quality checks decrease errors, enhance consistency, and drive higher customer satisfaction.
Successful smart manufacturing integration
Transitioning effectively to smart manufacturing requires careful attention to the following key areas.
Financial and investment planning:
- Plan upfront for high initial capital investment, but anticipate long-term gains through increased productivity and reduced operational costs.
- Employ financial modeling tools (e.g., ROI calculators, scenario planning software) to forecast and track benefits.
Talent and workforce management:
- Focus on upskilling employees in critical skill sets such as data analytics, cybersecurity, robotics programming, and AI management.
- Create structured, company-wide training programs emphasizing continuous learning and adaptability.
Change and risk management:
- Proactively identify and mitigate risks associated with interconnected systems using robust cybersecurity frameworks.
- Foster organizational cultures that embrace continuous improvement and innovation to overcome resistance to technological change.
A practical roadmap
Manufacturing leaders require a clear, actionable roadmap for transitioning to smart factories. We typically recommend a phased approach for our clients.
At a very high level, that could look a little something like this:
Assessment and readiness (1-3 months)
- Conduct an internal audit of current processes.
- Use gap analysis and benchmarking tools.
Pilot and testing (3-6 months)
- Launch pilot projects targeting specific production lines or processes.
- Evaluate pilot results, adjusting strategy based on early learnings.
Scaling and integration (3-12 months)
- Scale successful pilot programs across additional lines or facilities.
- Invest strategically in advanced robotics, AI systems, and infrastructure.
Optimization and continuous improvement (ongoing)
- Regularly collect, analyze, and act upon production data.
- Continuously update technology, processes, and training to maintain a competitive advantage.
Considerations and risk mitigation
Adopting new technologies always carries risks. Smart manufacturing leaders should proactively address the following common challenges.
Resistance to change: Actively communicate the vision and benefits of smart factories to foster organizational buy-in.
Financial Investment and ROI: Although upfront investments can be significant, model ROI clearly, leveraging phased implementation to demonstrate tangible short-term gains.
Risk management: Develop a robust cybersecurity strategy alongside digital transformation efforts, mitigating risks associated with increased connectivity.
Anticipating future trends in smart manufacturing
Looking ahead, several business transformation trends will continue to shape the smart manufacturing landscape.
Here are some to keep an eye on:
Digital Twins: Digital replicas of manufacturing systems will become mainstream, enabling real-time virtual experimentation without disrupting live production environments.
Edge computing and real-time analytics: Leaders must prepare for greater reliance on immediate, edge-based data processing, providing unparalleled operational responsiveness.
Augmented reality (AR) and virtual reality (VR): Increasingly common AR/VR-based training and operational support will speed workforce reskilling and enhance remote manufacturing operations.
What’s next?
The rise of smart manufacturing represents both a profound shift and an unprecedented opportunity.
Manufacturing leaders who embrace AI and automation, plan phased implementations, and carefully manage business transformation will remain at the top.
The path forward requires bold leadership, strategic clarity, and decisive action. Want to learn more about how Ascension Group can help guide your business transformation?