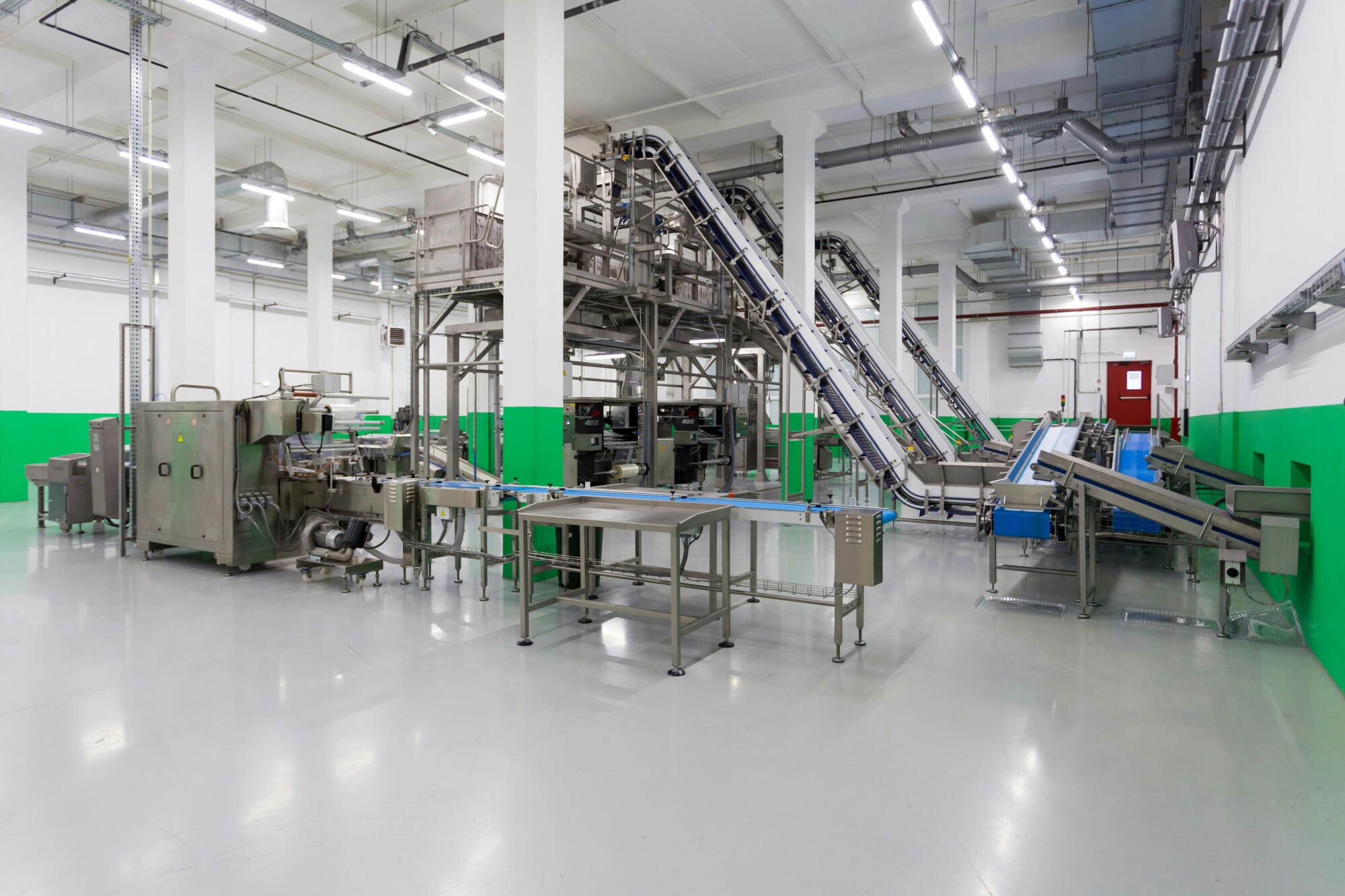
Manufacturing efficiency is broken. Here’s how to fix it
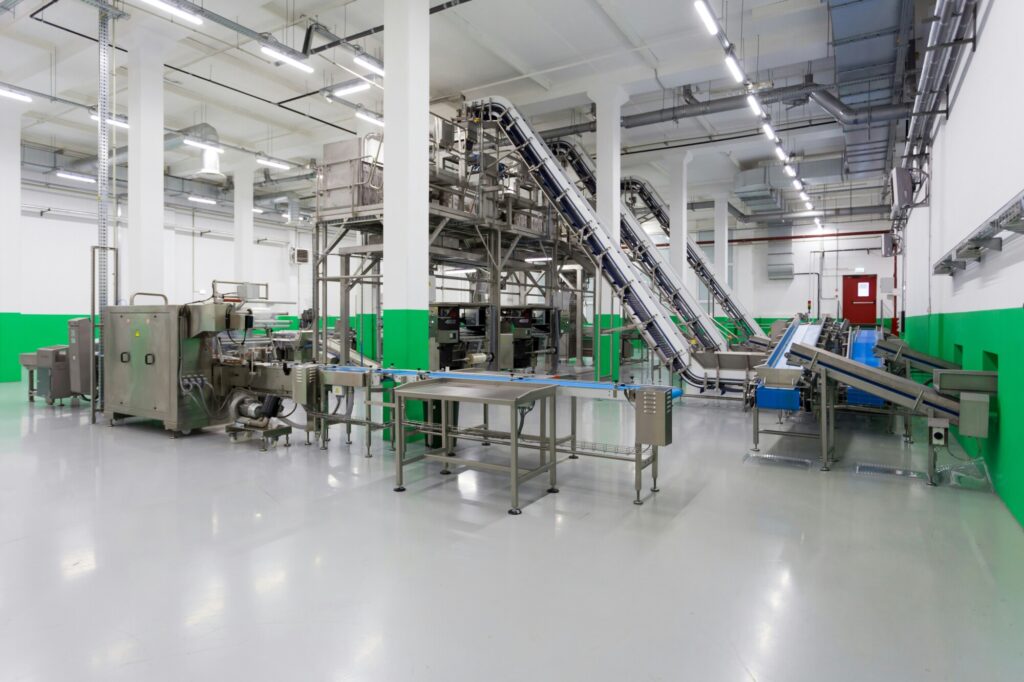
For decades, manufacturers have been sold the idea that manufacturing efficiency is about cutting costs; slashing headcount, squeezing suppliers, and racing to the bottom.
But that’s not efficiency. That’s short-term thinking disguised as strategy.
Real efficiency isn’t about spending less; it’s about producing more with what you have, reducing friction, and optimizing systems for sustained profitability.
If you’re only focused on cost-cutting, you’re missing the point.
The real game is about operational excellence, leveraging technology, and building a culture where efficiency is second nature; not just another quarterly goal.
Conduct a brutally honest process analysis
Most manufacturers think they understand their workflows. And most are wrong.
They measure success based on outdated KPIs or, worse, gut feelings.
Before implementing any manufacturing efficiency initiative, you need a clear, data-backed view of your current operations. That starts with:
- Baseline metrics: Conduct deep-dive audits, map workflows, and establish performance benchmarks.
- Industry benchmarking: Compare yourself to market leaders, not just competitors in your weight class, but the best in the business.
- Bottleneck identification: Use root cause analysis (value-stream mapping, digital twin) to identify and eliminate waste. Hint: Your biggest inefficiencies are often hiding in plain sight.
Get better at data
If you’re not measuring, you’re guessing. And in manufacturing, guessing is expensive.
KPIs should go beyond surface-level metrics. You need:
- Overall equipment effectiveness: Tracks availability, performance, and quality in a single metric.
- Cycle time & throughput efficiency: The pulse of your production line.
- Defect & quality rates: Efficiency without quality control is a recipe for recalls.
- Inventory turnover & waste metrics: Holding excess inventory is just tying up capital.
Stop paying lip service to lean manufacturing
Too many companies claim to “embrace lean” as part of their manufacturing efficiency plans, but in reality, they cherry-pick convenient tactics while ignoring the culture shift required for real business transformation.
Lean isn’t about doing more with less. It’s about doing better with what you have.
Automation is no longer optional
Manufacturers who resisted automation over the last decade of digital transformation are losing. Strategic technology adoption isn’t about replacing people; it’s about enabling and empowering them to do more.
Tech is your competitive advantage — but only when you actually use it.
Empower your employees
Efficiency isn’t just about machines. It’s about people. Your workforce needs to be empowered, trained, and engaged in driving improvements.
Cross-training and upskilling: Reduce single points of failure by ensuring employees can step into multiple roles.
Employee-led problem solving: If you’re willing to listen, some of your best efficiency solutions are inside the heads of frontline workers.
Performance incentives: Reward productivity gains and quality improvements, not just cost-cutting.
Rethink your supply chain strategy
Your supply chain is either an asset or a liability. And the only difference is how well you optimize it.
- Supplier evaluation: If your vendors aren’t evolving, they’re holding you back.
- Advanced inventory management: Demand-forecasting tools can reduce waste by 15–20%.
- ERP & MRP systems: If you’re still relying on spreadsheets, you’re already behind.
Maintenance is not an afterthought
Most manufacturers still treat maintenance as a necessary evil instead of a competitive advantage.
- Predictive maintenance: Using sensors and AI to prevent breakdowns before they happen is a game-changer.
- Preventative maintenance programs: Scheduled maintenance isn’t a cost; it’s an investment in uptime.
- Downtime metrics: Tracking mean time between failures can save you millions in lost production.
If you want to truly improve efficiency and reduce costs, stop looking for shortcuts and start making systemic, strategic changes. Manufacturers who embrace data, automation, lean principles, and employee-driven improvements will dominate. Those who don’t will be outpaced, outperformed, and eventually obsolete.
If you’re not sure where to start or you’re looking for a fresh perspective, strategic advisors can provide useful insights to help you get unstuck.